鋼橋の形状モデル
橋梁は何次元の構造物でしょうか。形状は3次元ですが、車のボディーや機械部品等と同じ3次元製品と考えて良いのでしょうか。
また、橋梁はいくつの単位を持っているのでしょうか。
プレートガーダーをモデル化された棒で扱う設計では単位はN/mm2です。形状を持った膜で部材を扱う原寸では単位はmmです。
原材料の鋼板はt、塗装面積はm2、そして最も重要な単位は¥です。様々な特徴を持つ橋梁に対して、主に原寸工程から発信される製作情報に対し、
物作りの側面からスポットを当て、解説して行きます。
次元は空間の広がりを表す一つの指標です。座標が導入された空間で物の形が表現されます。一般的に工業製品は3次元空間上で定義され、
製品の3次元形状モデルとそれを投影した平面図、正面図、立面図の関係に矛盾は生じません。
そのため形状モデルをCADで作成して試行錯誤を繰り返す設計が主流で、製造と密接に結びついたデジタル情報の交換が普及しています。
それに対し道路は自然条件や地理的要件などの周辺環境と密接に関係しており、その線形は車の動きと関係する道路線形で表現されます。
道路の一部である鋼橋もその形状は道路線形と同様に定義されます。XY面の平面線形とUZ面の縦断線形です。
2つの2次元線形の組合わせで3次元が表現される2.5次元の空間です。ここでは3軸を固定し静的な視点から眺めた3面図に代わり、
線形に沿って変化する動的な視点から眺めた平面図、縦断図、断面図が使われます。従って鋼橋は一般の工業製品のような3次元形状モデルではなく
2.5次元形状モデルとして扱われます。
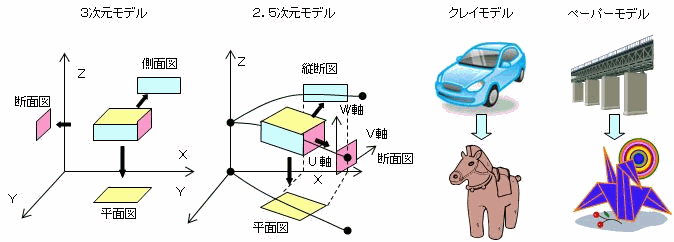
3次元形状モデルと2.5次元形状モデルの違いは粘土細工と折り紙に例えることができます。 クレイモデルで表現される車のボディー等と違い、鋼橋は平面と平面を曲げ加工した緩やかな曲面で構成されるペーパーモデルで表現できます。 一枚の紙から作られる折鶴のようなモデルです。
原寸工程
原寸。建築では現寸、英語ではFull Scale Drawingと表現されますが、橋梁の原寸とはどのような工程でしょうか。
物づくりのための工程であればなぜ自動車など他の工業製品の製作にはこの工程が無いのでしょうか。
鋼橋の設計図面は完成時の形状・寸法で表示されています。
そのため実際の製作に当たってはキャンバーや溶接による収縮、ひずみなどを考慮する必要があります。
原寸作業はこれらの影響を考慮した展開計算により寸法を決定し、製作に必要な資料の作成を行う一連の作業です。
鋼道路橋施工便覧では原寸作業の目的を次のように定義しています。
(1)部材、部品の正確な寸法の決定
(2)定規、型板、NCデータ等の罫書資料、あるいは加工、仮組立 等の指示伝票の作成
(3)各部品、部材の取り合い関係、施工上の支障がないかどうかについての検討
一般の工業製品では形状モデルをCADで作成して、試行錯誤を繰り返す設計が主流です。
ここでの製図は試行錯誤を伴って寸法を決めるという設計業務に当たり、製造と密接に結びついたデジタル情報が交換されます。
それに対し鋼橋の設計では、構造寸法が設計計算段階で確定します。
ここでの製図は設計結果を人が見て理解しやすくするための視覚化の方向へ発展してきました。
冗長さを避けるため対称構造の半分は省略され、同形状で寸法が異なる部材は表で表現されます。
部材の板厚を2本線で表現するきめ細かさや、視点を動かして見える面と見えない面を同じ面に描くなど、製図というよりも絵に近い表現がされています。
従って設計図面をそのまま加工図面として採用することはできません。
設計図の内容に施工法を折り込み、製作工程で利用できる資料を作り出す原寸作業が不可欠な工程となります。
昭和40年代に入るとそれまでの床書原寸に代わり、コンピュータを利用したNC原寸が始まりました。
初期のシステムは鈑桁の形状を展開計算して、型板や定規を作成する機能の限られたものでしたが、
工作機械のNC化に伴い製作情報全般を扱うシステムとして発展してきました。
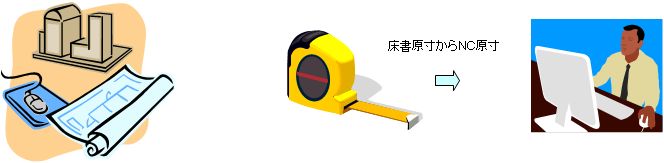
製作情報システム「MASTERSON」
製作情報システムは交通インフラに例えると航空機や鉄道に相当します。効率よく大量の情報を遠く離れた目的地近くまで運んでくれます。 これに対してCADは車に相当します。生産性は高くないですが、情報を加工して最終の目的地まで届けてくれます。今日、これら製作情報システムと CADを複合的に運用し、出力をCAD編集システムやエクセル等で加工することにより各社固有の製作情報処理がなされています。
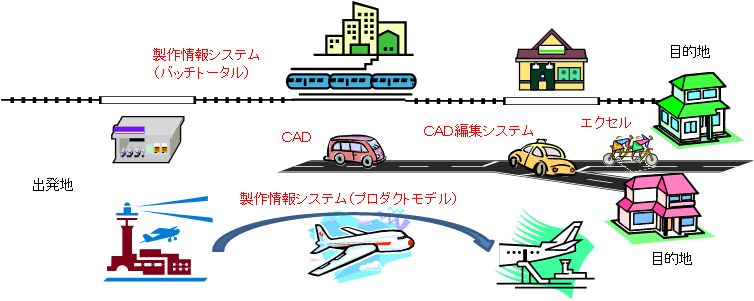
製作情報システムはシステム形態により数値データでデータベースを構築するバッチトータルシステムとCADで3次元モデルを構築するプロダクトモデルシステムに
分類されます。ここでは机上でデータを作成して照査を行うだけで、原寸から仮組立までの一貫した製作情報が得られるバッチトータルシステムの
「MASTERSON」にスポットをあて、システムの詳細について解説していきます。
鋼橋は一橋毎に定められた条件のもとで、最適な設計が要求される多品種一品生産の製品です。従って、標準部材をアッセンブルして製作することはできません。
このシステムでは鋼橋を構成する部材を共通部材に分類します。例えば主桁のウェブ、フランジは「主桁パネル」に分類されます。ダイアフラムやブラケットは
「サブブロック」に、また水平補剛材、垂直補剛材、縦リブなどは「取付部材」に分類されます。そして分類された種類毎に部材形状を決定するロジックを考えて
プログラム化されています。
MASTERSON【線形】
設計の線形計算結果には、3次元形状モデル作成に必要な全ての点の座標値は求められていませんので、補間計算により求める必要があります。
そのために、独立点と称する座標値が既知の点を結んで補間ラインを作り、独立点間に縦断線形要素と平面線形要素を定義します。
それら線形要素は直線、放物線、3次曲線、円の4種類とし、線形が連続の場合、接線を共有するものとします。
次に補間ライン上に、独立点間距離に対する比率、または独立点からの距離により従属点を配置して、
3次元形状モデル作成に必要な全ての格点を補間します。
1つのX座標値に対して2つのY座標値が存在するループ橋の線形に対しては、ローカル座標軸を設けることにより扱えるようになっています。
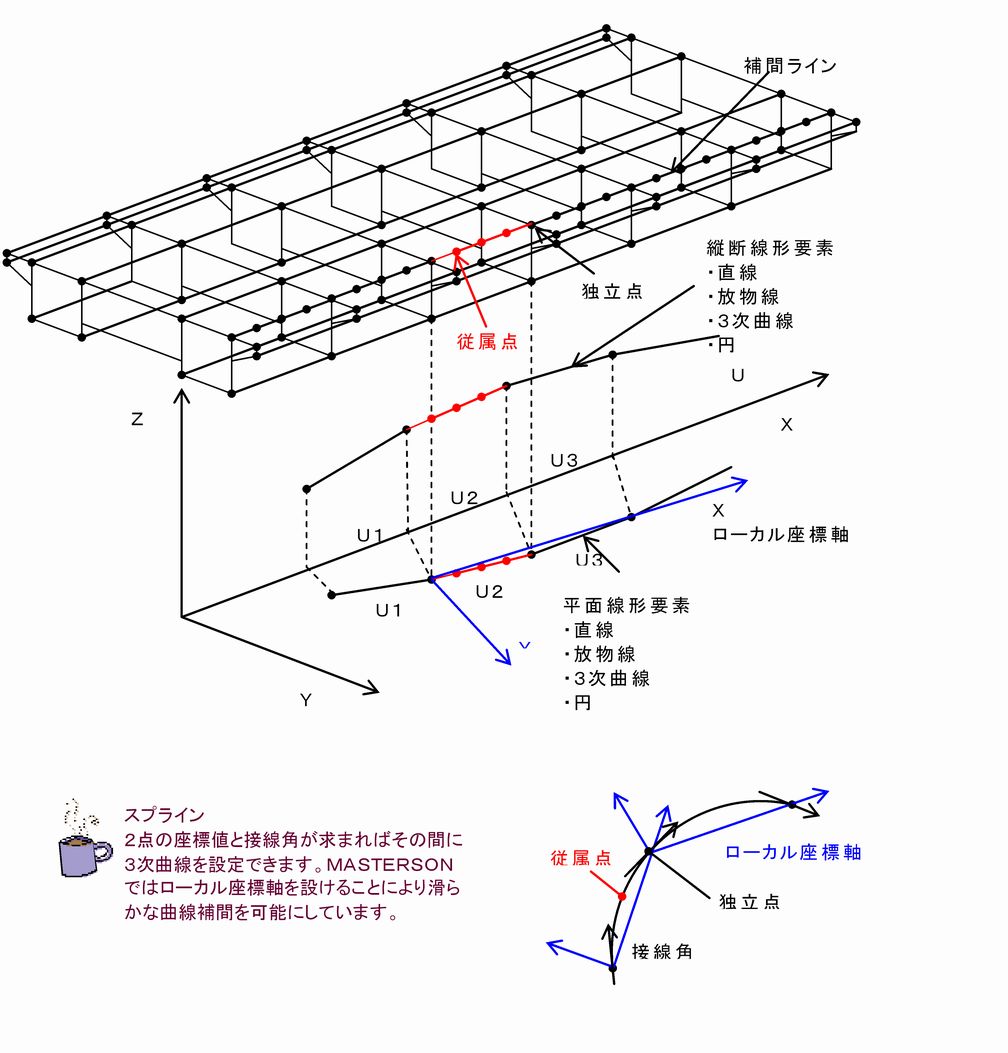
MASTERSON【キャンバー】
構造物の骨組線をキャンバー基準線として定義し、骨組線と連動する補間ライン上の格点の架設時、仮組時座標値を決定します。
キャンバー値の決定に際しては、下図に示す3並進、3回転を取り扱えます。
【3並進】
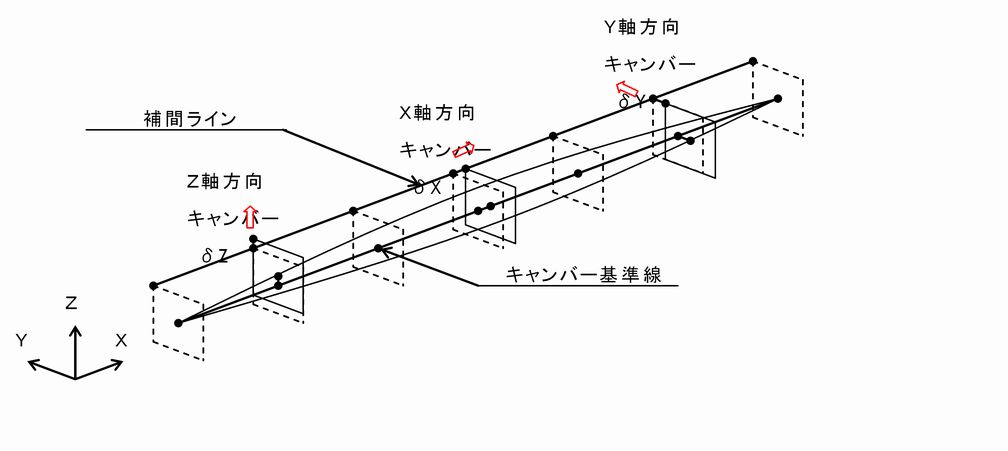
【3回転】
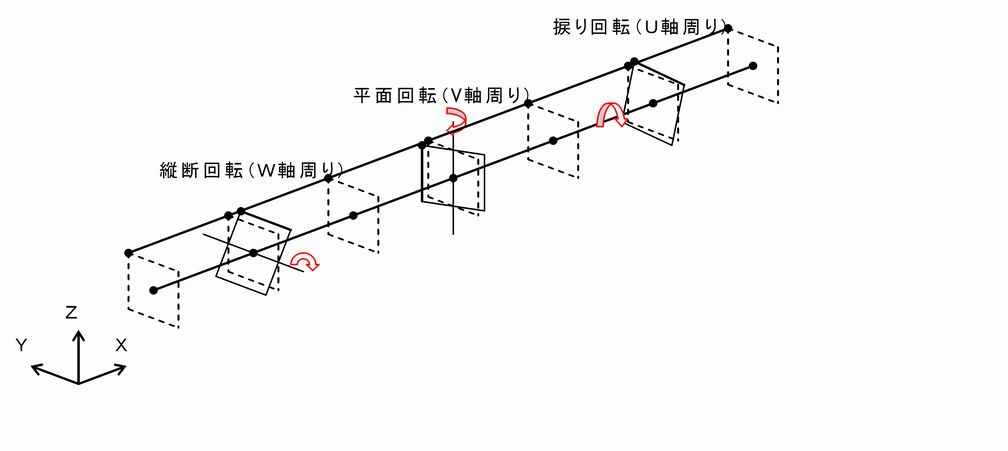
溶接による変形を考慮した拡大や上げ越しキャンバーはそれぞれの補間ライン上で計算し、原寸時座標値を決定します。
【上げ越し】
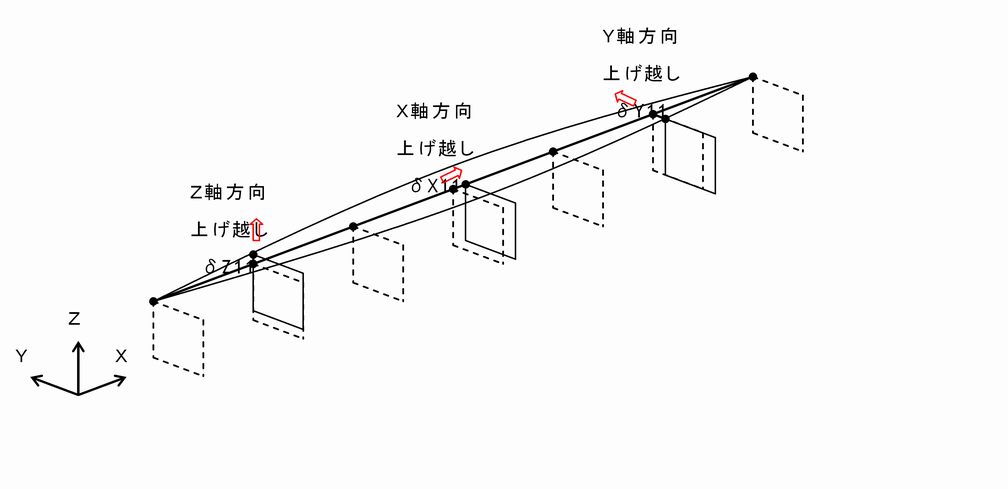
【伸ばし】
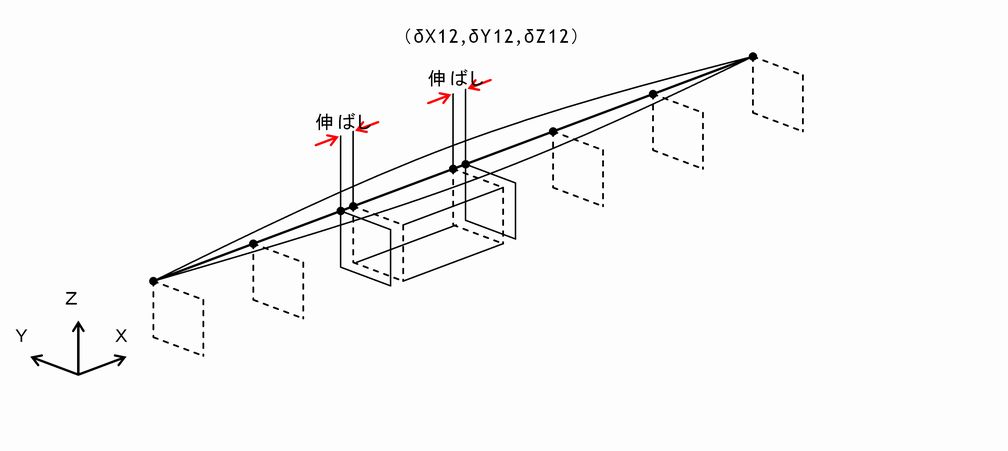

MASTERSON【主桁パネル】
【主桁パネルの階層構造】
線形、キャンバーは「点の世界」ですがここから「面の世界」に入ります。
主桁を構成する補剛パネルは、空間におけるポジションと受け持つ力の種類によりウェブ、フランジなどの名前がついています。
そのような「色」を消して、構造物を補剛パネルの集合体としてモデル化し、以下の階層構造を設定します。
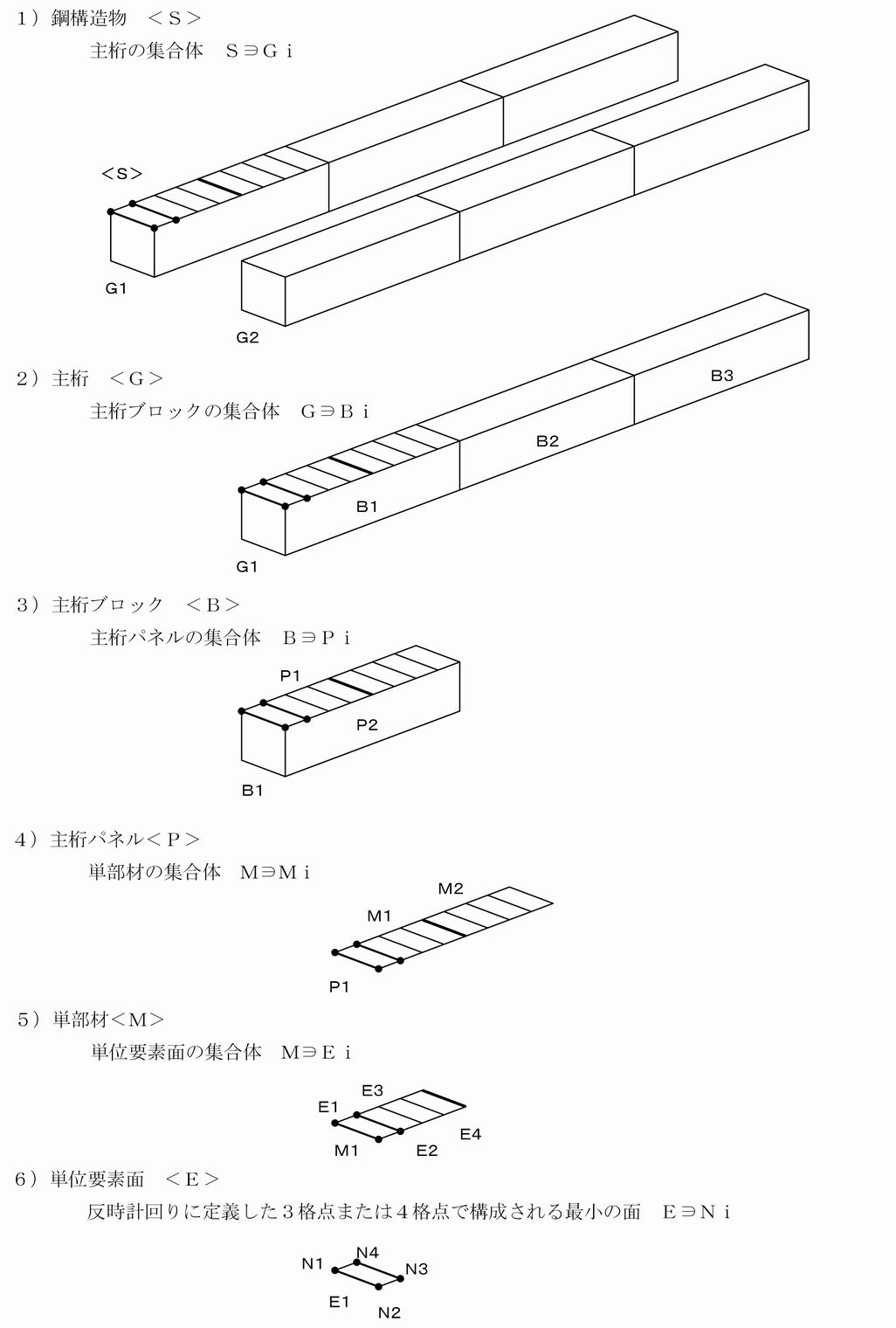
主桁パネルと格点の関係を一つのモデルで表現したのが次の図です。
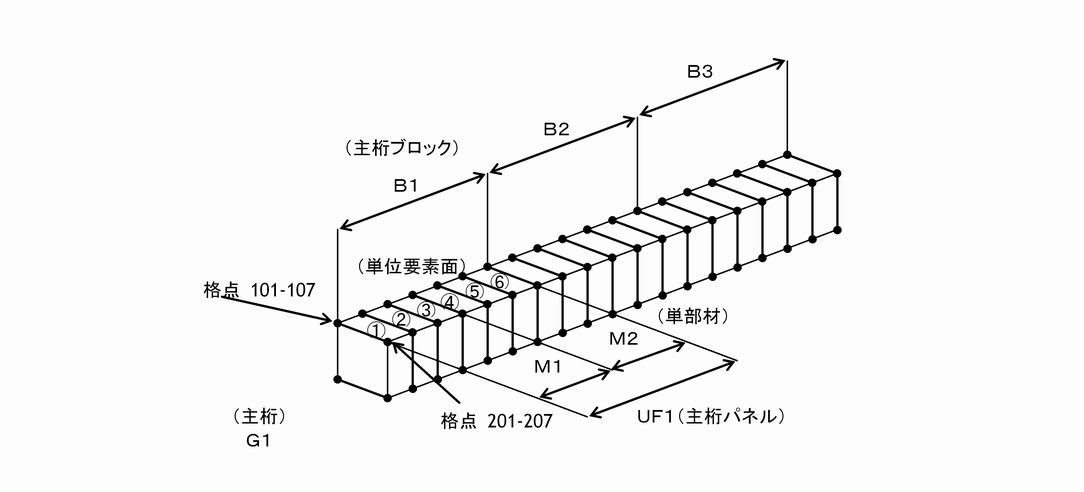
【主桁パネルの展開】
「面の世界」では単位要素面は4格点または3格点からなる薄い膜ですが、格点に座標値を与えることにより初めて形状が決まります。
3次元の座標値には線形で計算される完成時座標値のほかに、キャンバー、上げ越し、伸ばしを付加した
架設時、仮組時、原寸時の合計4ステージの座標値があります。
格点の4ステージの3次元座標値
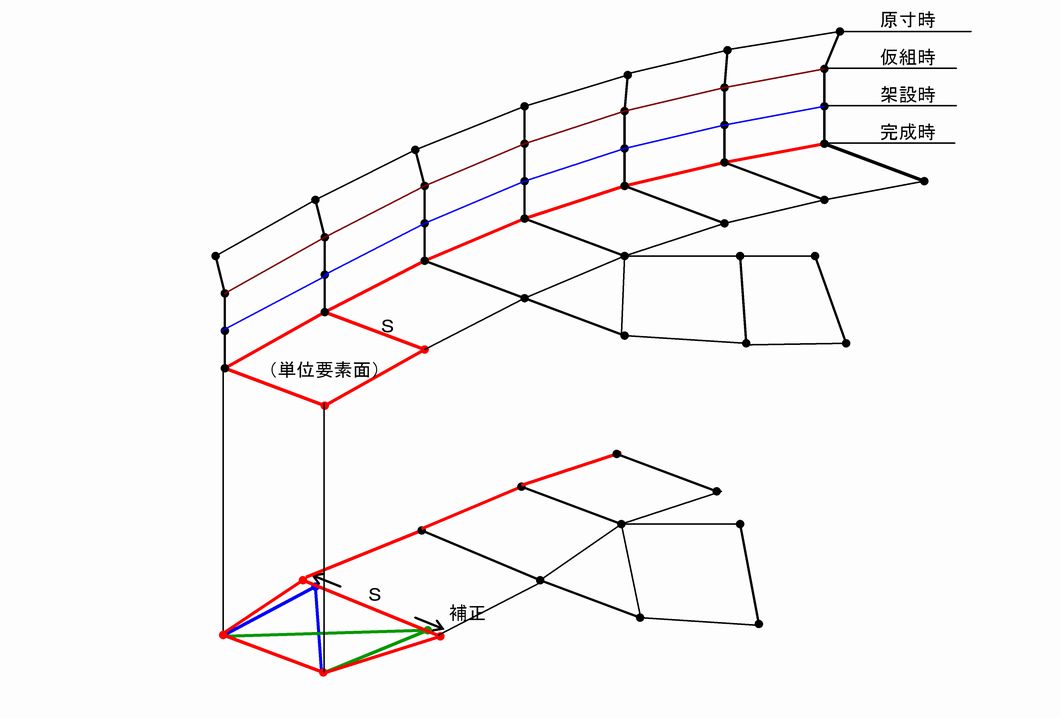
「面の世界」には3次元と2次元の2つのフェーズがあります。3次元から2次元へフェーズを変換するプロセスが展開です。
展開の方法は上図に示すようなたすき展開です。青と緑の2つの三角形を作り平面に下ろします。
次に平面の2つの三角形の頂点を結んだ線分の長さが、同じ2点間の空間の距離に等しくなるように補正します。
これを繰り返して主桁パネルの展開座標値を求めます。MASTERSONでは3角形の単位要素面を
定義することにより、主桁が分岐するような任意形が扱えるようになっています。
【主桁パネルの拡大】
展開された平面上で歪拡大、外縁拡大を行い、取付部材配置の基準になる歪拡大座標値と、部材切断線になる外縁拡大座標値を決定します。
この段階で単位要素面を構成する格点は次の座標値を持つことになり、その形はどの座標値を採用するかにより決まることになります。
【3次元の座標値】
完成時座標値/架設時座標値/仮組時座標値/原寸時座標値
【2次元の座標値】
展開座標値/歪拡大座標値/外縁拡大座標値
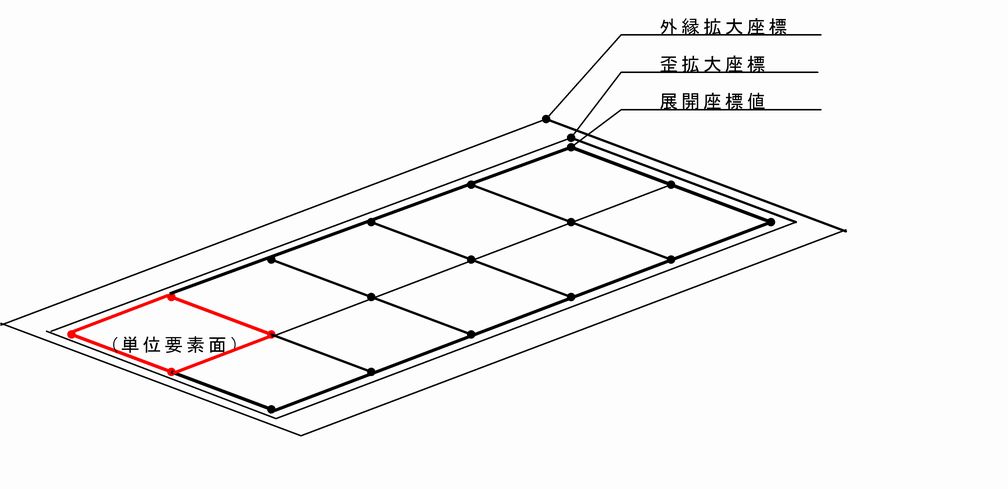

MASTERSON【サブブロック】
【サブブロックの階層構造】
サブブロックとはダイアフラム、横桁、ブラケット、対傾構などの床組の総称です。竹の節のような部材で、
形状は線形に応じてパラメトリックに変化します。
住所の何丁目何番地に相当する横断位置、横断通り上に配置されるサブブロックに以下の階層構造を設定します。
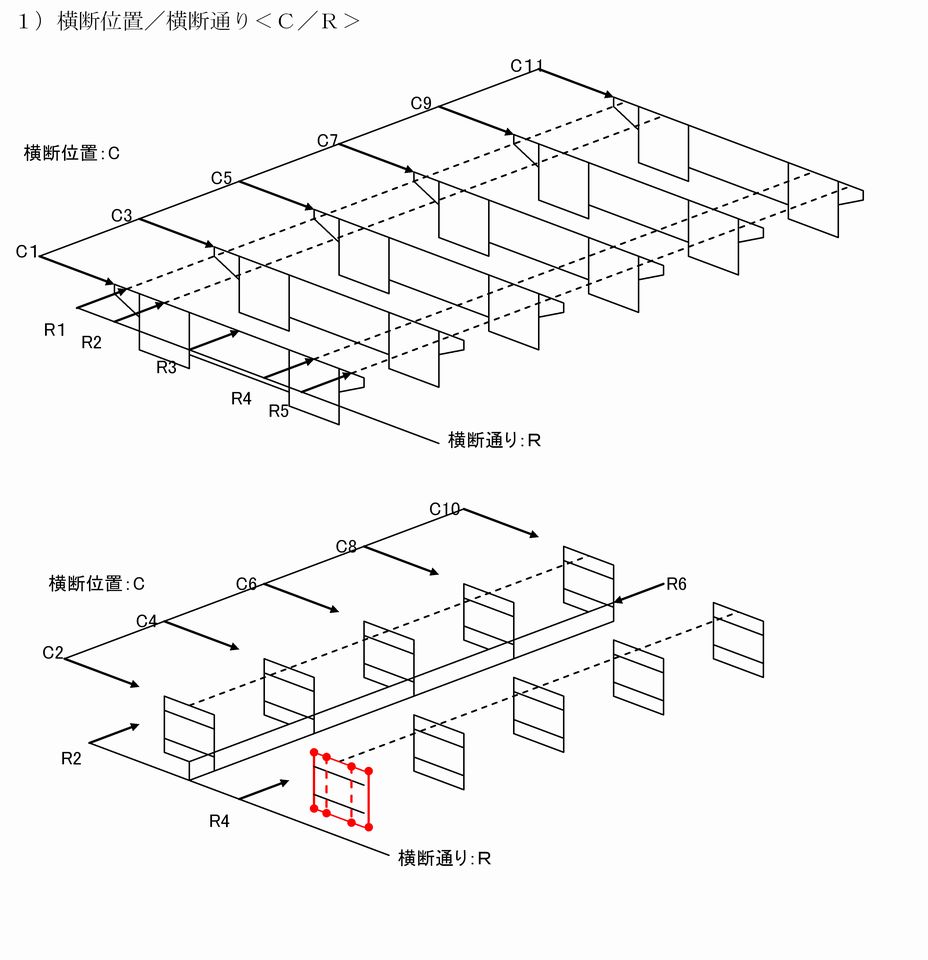
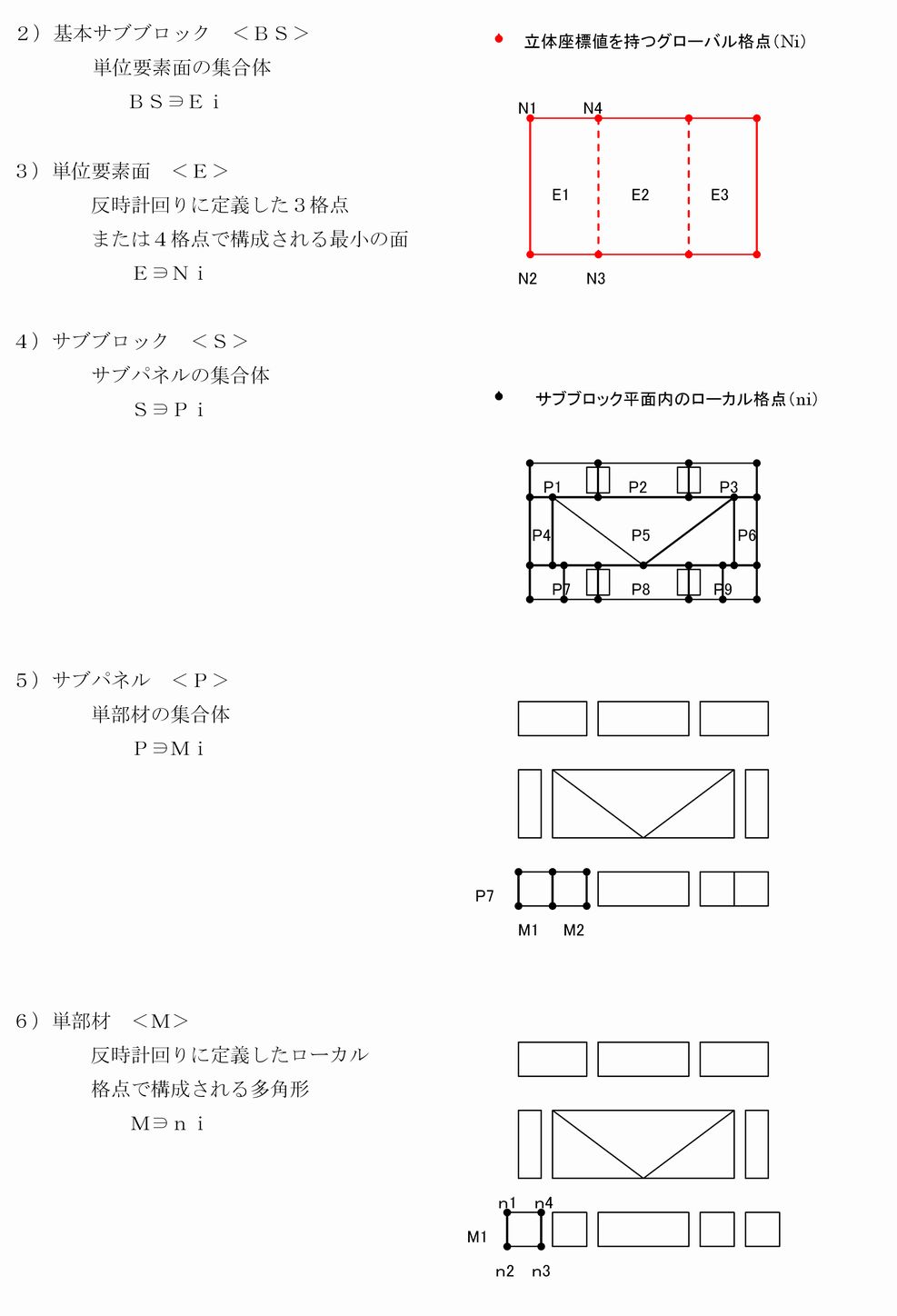
【基本サブブロックの展開】
サブブロックと格点の関係を表現したのが次の図です。この段階でのサブブロックは基本サブブロックと呼ばれ、
立体座標値を持つグローバルな4格点または3格点で構成される単位要素面(Ei)の集合体です。
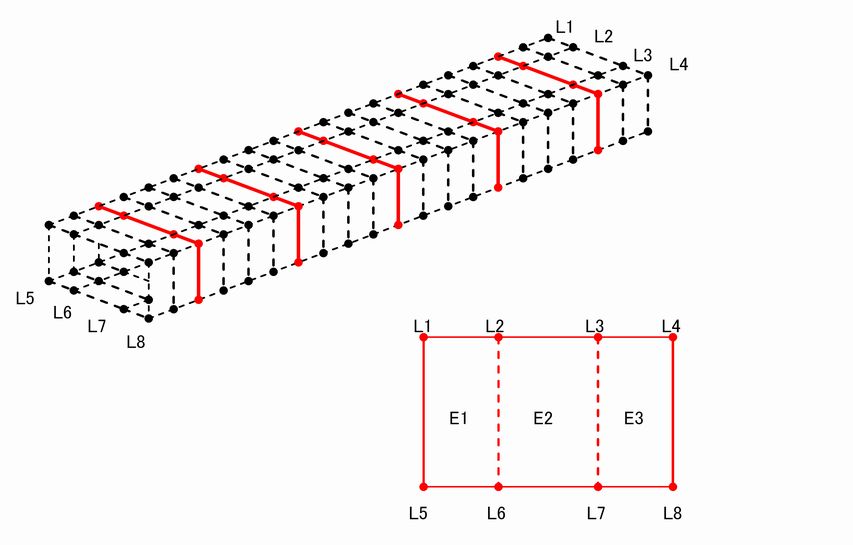
主桁パネルと同じ方法で基本サブブロックの単位要素面を展開します。3次元の座標値には線形で計算される完成時座標値のほかに、 架設時、仮組時、原寸時の合計4ステージの座標値がありますので、どのステージを選択するかにより展開座標値が変わります。
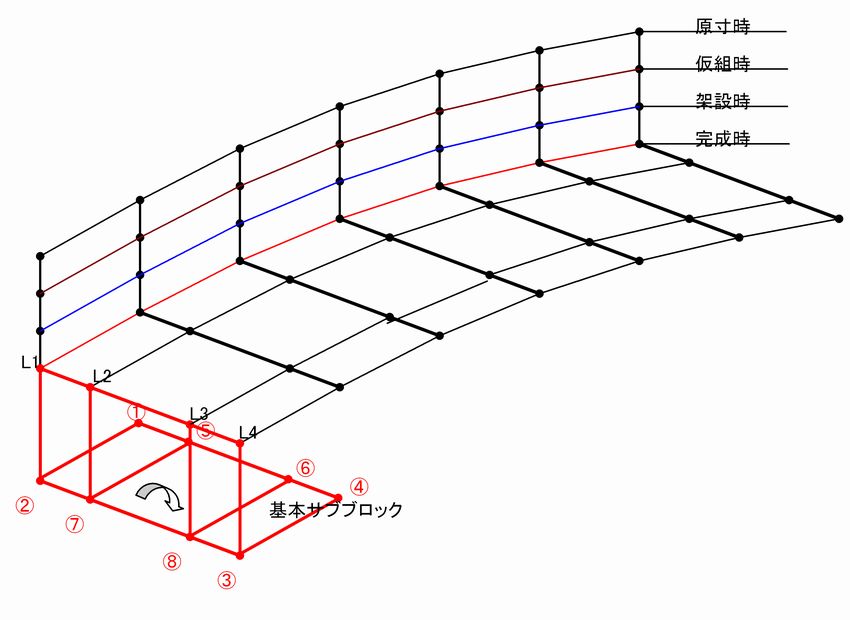
【ローカル格点の作成と部材形状の定義】
基本サブブロックの展開された平面上にサブブロックを構成する部材の形状を決めるために必要なローカル格点を発生させます。
このローカル格点を反時計回りに結ぶことにより部材を形作って行きます。
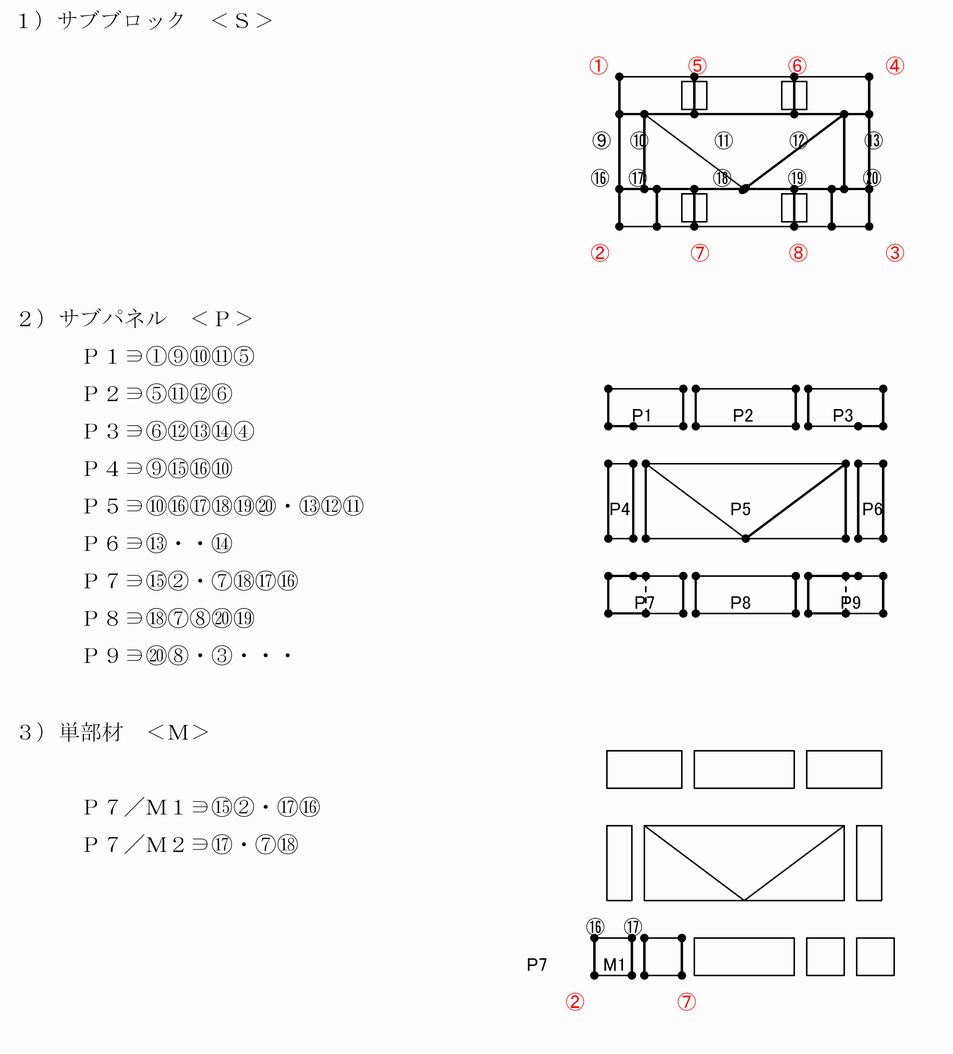
【サブブロックの拡大】
サブブロックには溶接歪みを考慮して全ての格点が拡大される歪拡大と、サブパネル単位に外形格点のみが拡大される外縁拡大の2種類の拡大を設定します。
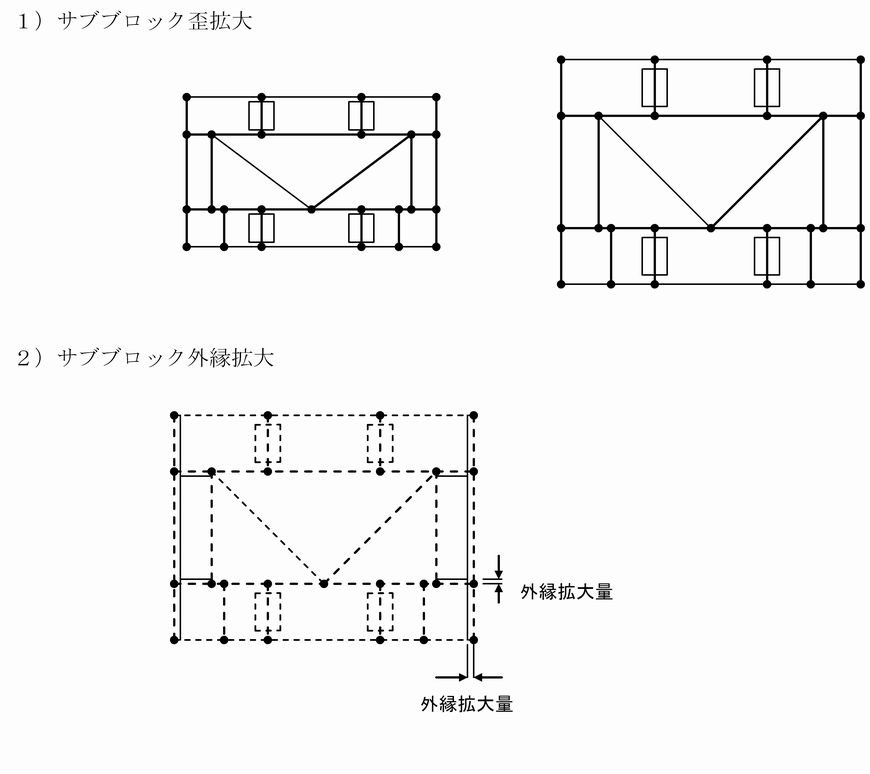
MASTERSON【主桁添接板】
【主桁添接板の階層構造】
サブブロックと同じように主桁添接位置、添接ラインに番号付けを行い、添接ライン上に添接板の塊の添接ブロックが配置されるモデルを考えます。
主桁添接ラインはウェブ、フランジなどのパネルの種類ごとに橋軸方向と橋軸直角方向の2種類のラインを設定します。
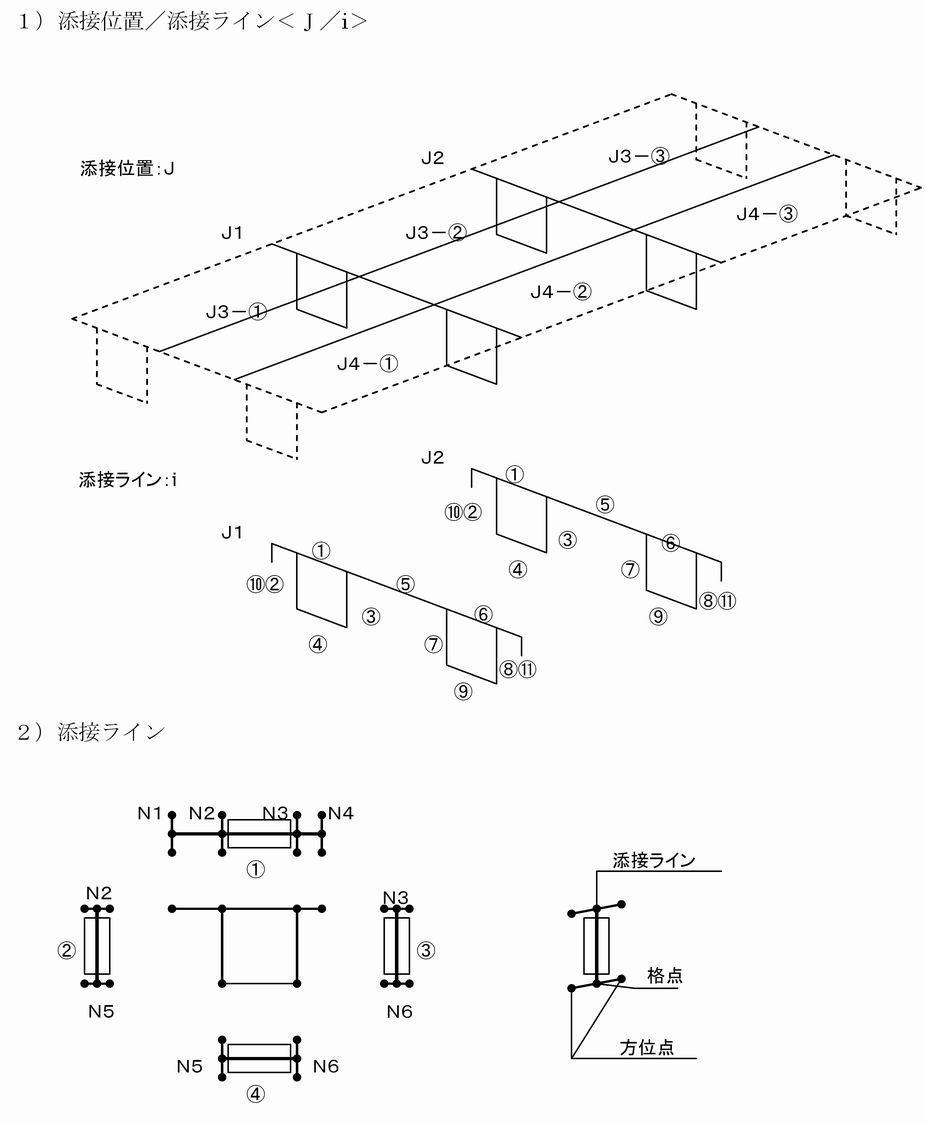
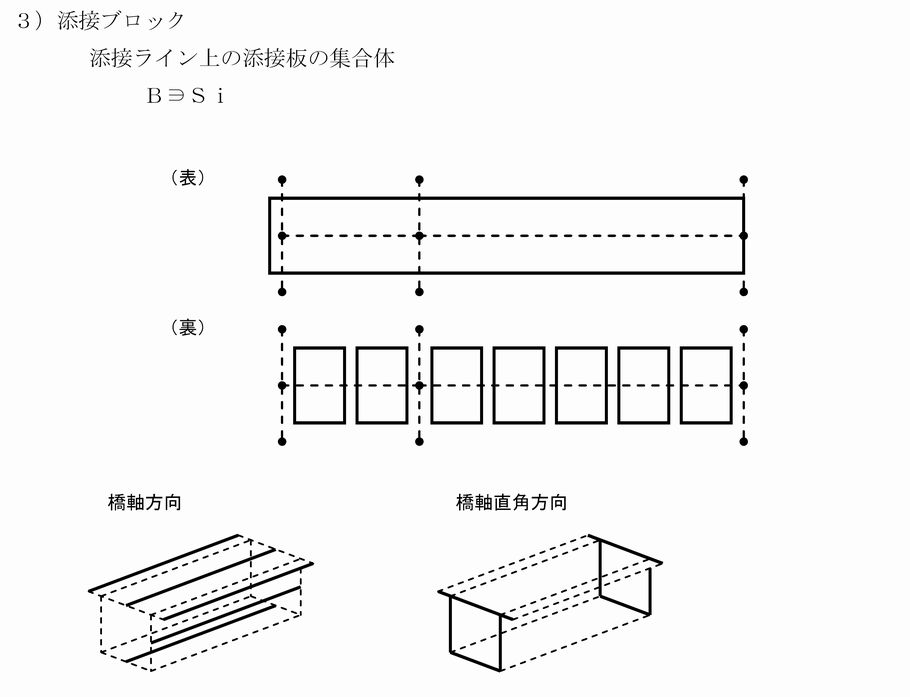
【添接ラインの展開】
添接ラインは1本のライン上の格点、または複数のライン上の格点を結んで定義します。添接ライン上の格点は、左右両方または片方に方位点を持ちます。

添接ラインを構成する格点並びに方位点は、線形で定義される完成時座標値のほかに以下に示す立体座標値と展開座標値を持ちます。
完成時座標値に架設-完成間キャンバー、仮組-架設間キャンバー、原寸-仮組間キャンバーの組合わせを付加して、
展開時の立体座標値を求め平面展開します。
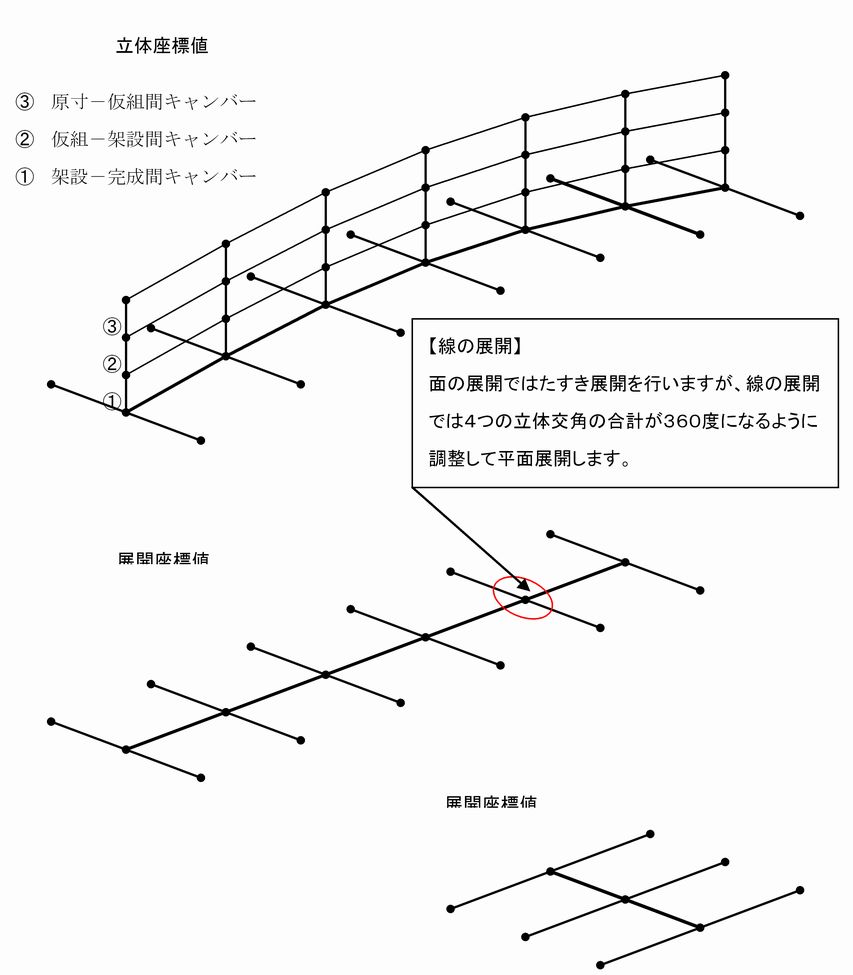
MASTERSON【取付部材】
【主桁パネルの取付部材】
主桁パネルを構成する単位要素面上にグリッド(格子)を定義します。全ての取付部材はグリッドを基準にして配置されます。
取付部材は形状決定方法の違いにより次の3つのグループに分類されます。
1)パネル上に配置されて長さが決まるような縦リブや補剛材のような部材
2)塗装用吊金具のように形状が最初から決まっていてパネル上に配置される部材
3)主桁の添接板のようにパネル形状と独立して形状決定され、パネル上に配置される部材

主桁パネルの取付部材には次のような種類があります。
1)主線材(垂直補剛材、水平補剛材、縦リブなど)
断面形状が決まっていて、パネル上に配置されて全ての形状が決定される補剛材
2)主線材フランジ(垂直補剛材フランジ、水平補剛材フランジ、縦リブフランジなど)
断面形状が決まっていて、主線材と共にパネル上に配置されて全ての形状が決定される補剛材フランジ
3)パネルフランジ(耳縦桁フランジなど)
断面形状が決まっていて、パネル上に配置されて全ての形状が決定されるフランジ
4)線材添接板(縦リブ添接板など)
全ての形状が決まっていて、主線材、主線材フランジ、パネルフランジを連結する添接板
5)附属線材(コネクションPL、吊金具など)
全ての形状が決まっていて、パネル上に板厚面が配置される部材
6)面材(コネクションPL、ソールPLなど)
全ての形状が決まっていて、パネル上に板面が配置される部材
7)ガセット(横構ガセット、コネクションPLなど)
横構との取合いで形状決定され、パネル上に板厚面が配置される部材
8)主桁添接板
縦横断線形で形状決定され、パネル上に板面が配置される部材
ガセットと主桁添接板は、パネル形状と独立して形状決定される部材であるため、主桁パネル取付部材とは別に定義します。
【サブブロック取付部材】
展開された基本サブブロック上にサブブロックの形状決定および取付部材配置のため、ローカル格点を定義します。
全ての取付部材はローカル格点を基準にして配置されます。取付部材は形状決定方法の違いにより次の2つのグループに分類されます。
1)パネル上に配置されて全ての形状が決まる補剛材のような部材
2)塗装用吊金具のように形状が最初から決まっていてパネル上に配置される部材
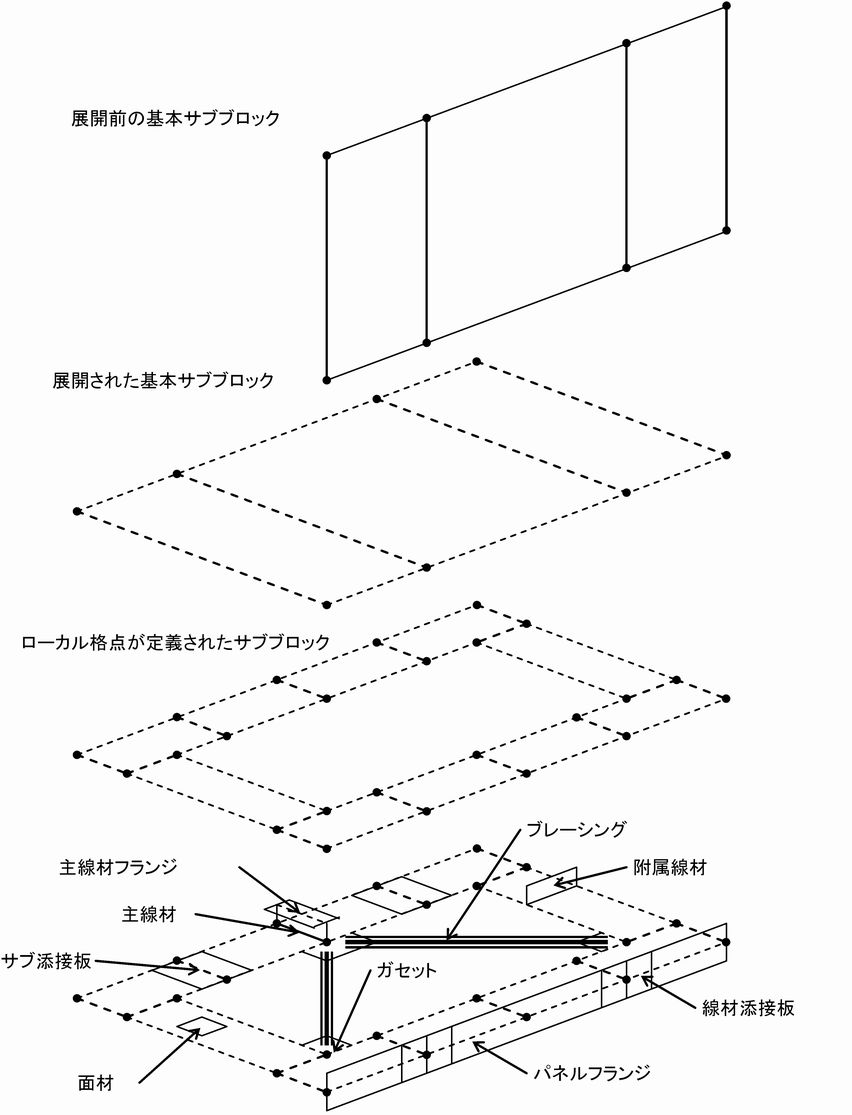
サブブロックの取付部材には次のような種類があります。
1)主線材(垂直補剛材、水平補剛材、補強リブなど)
断面形状が決まっていて、パネル上に配置されて全ての形状が決定される補剛材
2)主線材フランジ(垂直補剛材フランジ、水平補剛材フランジ、補強リブフランジなど)
断面形状が決まっていて、主線材と共にパネル上に配置されて全ての形状が決定される補剛材フランジ
3)パネルフランジ(横桁フランジ、ブラケットフランジ、縦桁フランジなど)
断面形状が決まっていて、パネル上に配置されて全ての形状が決定されるフランジ
4)線材添接板(フランジ添接板など)
全ての形状が決まっていて、主線材、主線材フランジ、パネルフランジを連結する添接板
5)附属線材(コネクションPL、吊金具など)
全ての形状が決まっていて、パネル上に板厚面が配置される部材
6)面材(コネクションPL、補強版など)
全ての形状が決まっていて、パネル上に板面が配置される部材
7)ガセット(対傾構ガセット、コネクションPLなど)
ブレーシングとの取合いで形状決定され、パネル上に板厚面が配置される部材
8)ブレーシング(上下弦材、斜材など)
断面形状が決まっていて、パネル上に配置されて全ての形状が決定される部材
9)サブブロック添接板
断面形状が決まっていて、パネル上に配置されて全ての形状が決定される添接板
MASTERSON【主桁ブレーシング】
主桁ブレーシング通りに配置されるブレーシング、ガセットに以下の階層構造を設定します。
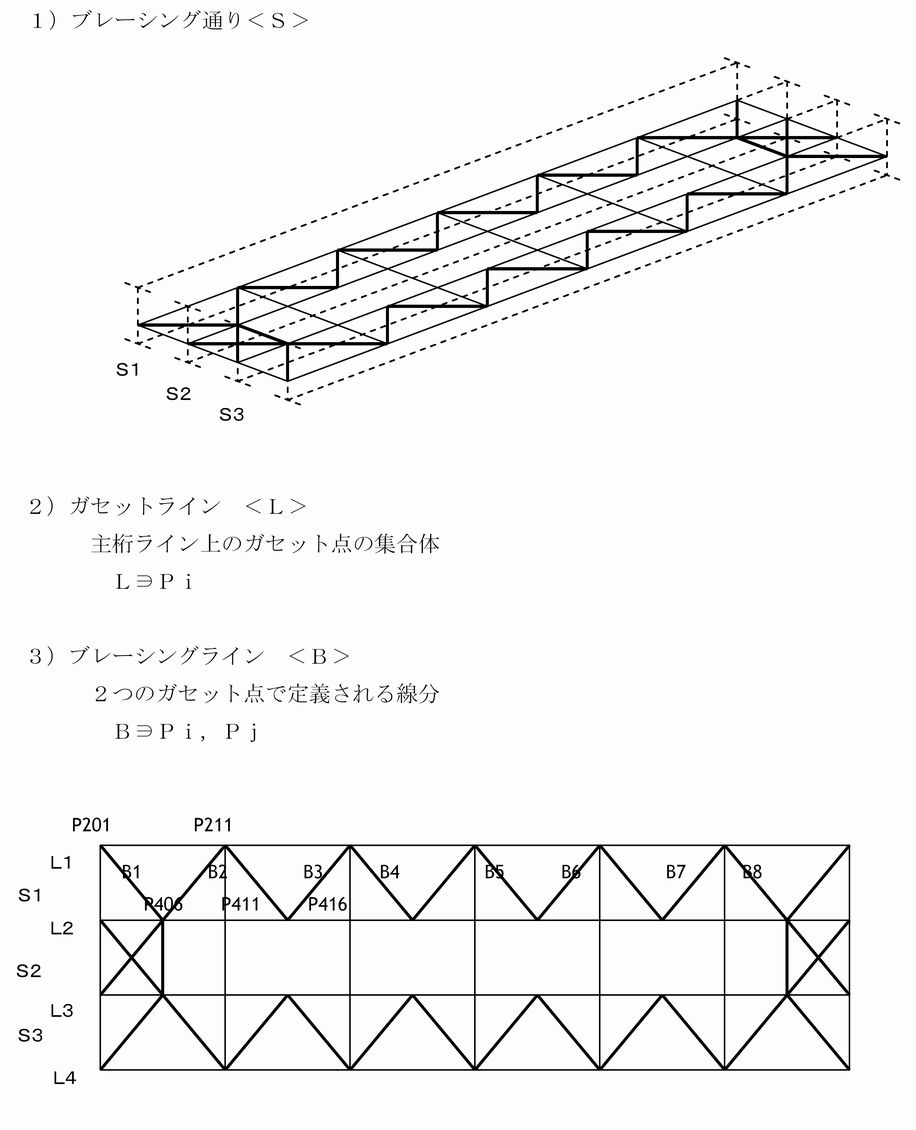
主桁ブレーシングの種類
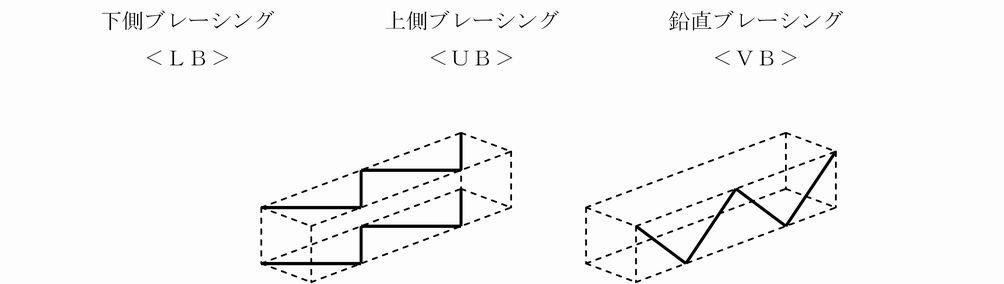
主桁ガセットの種類
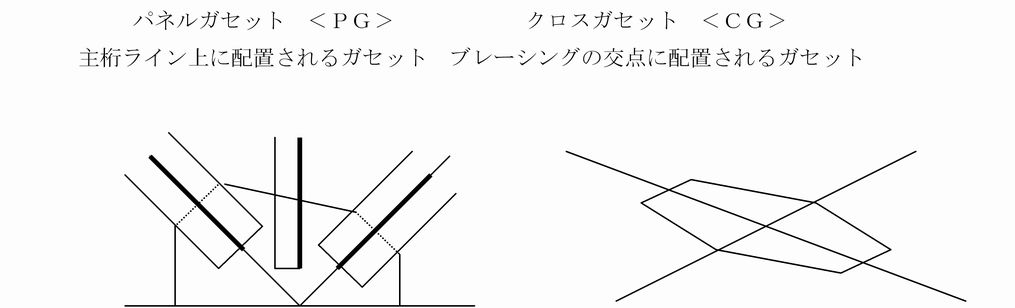
主桁ガセットで連結される部材の種類
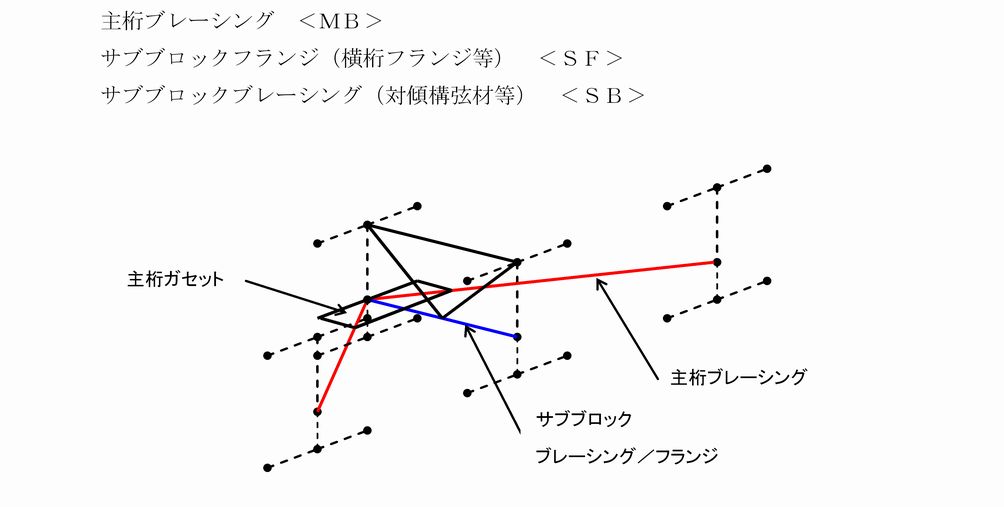
ブレーシングラインおよびガセットポイントと格点の関係
ガセットライン上のガセット点と前後の格点、シフト方向の方位点、およびブレーシング端点のガセット点を使ってガセット
およびブレーシングの形状を決定します。
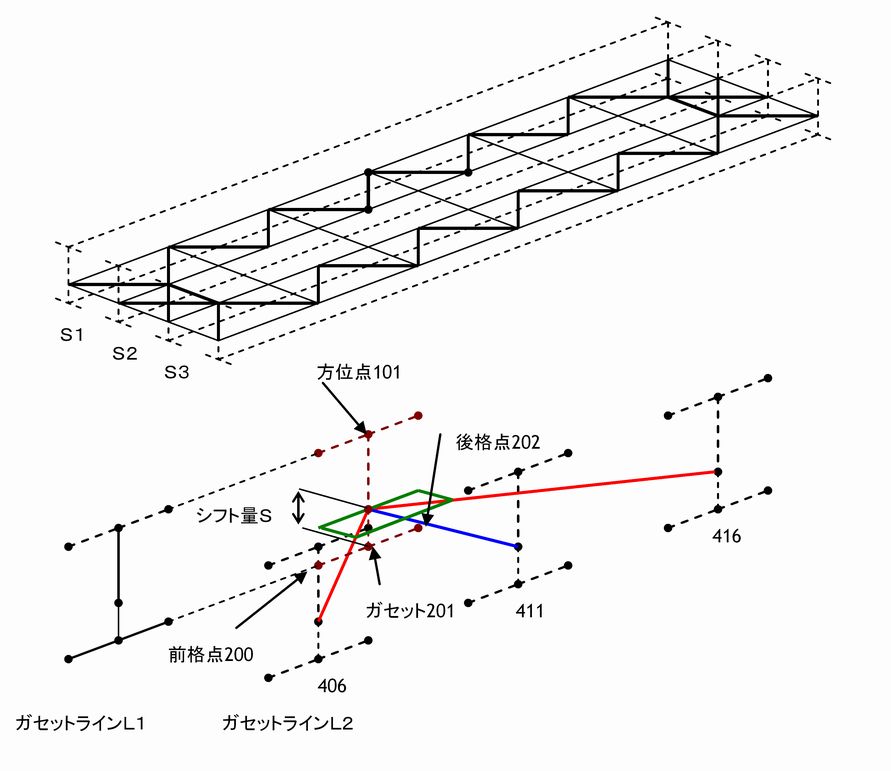
MASTERSON【システム構造】
システムは入力部、計算部、マスターファイル、出力部で構成されます。マスターファイルはDSファイルと呼ばれるISAM方式のファイルです。 ISAMとは高速にアクセスできるデータの格納方法の一つでIBMで開発されました。 計算部プログラムによる計算結果は逐次マスターファイルに書き込まれます。 出力部プログラムはマスターファイルに格納されたデータを読み込んで図面、テキスト、NC情報に加工します。 データには項目ごとに5つのキーが付けられており、そのキー番号で読み込み、書き込みが管理されます。
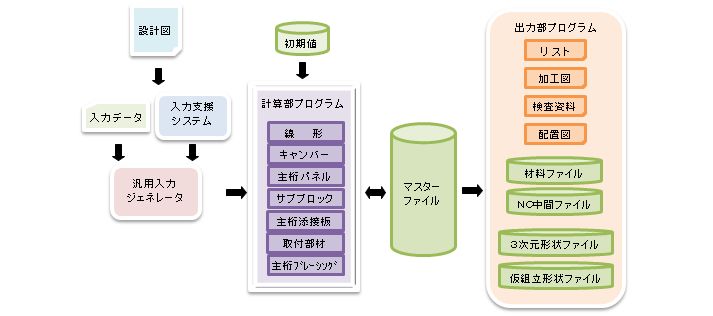
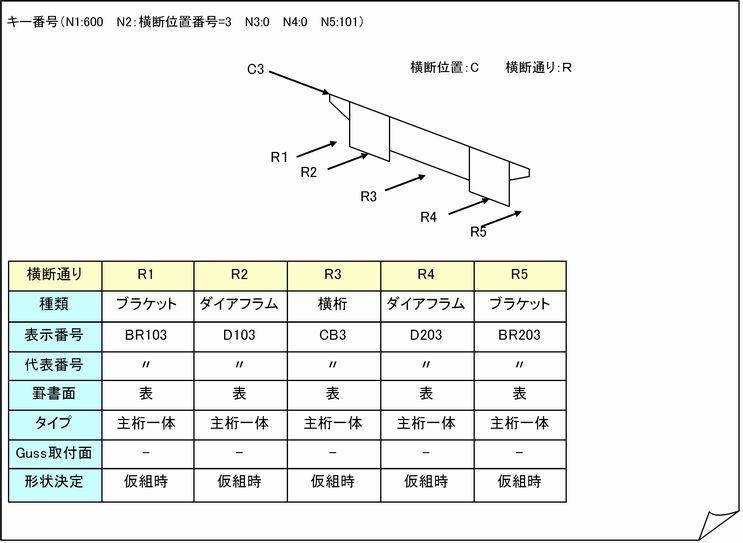
まとめ
これまで汎用の製作情報システム「MASTERSON」を例に鋼橋をモデリングするためのロジックについて解説してきました。
このシリーズのまとめとして情報の連携をキーワードに今後の製作情報の方向性を見て行きたいと思います。
製作情報システムにはフォートランで組まれた「MASTERSON」等の第1世代のシステムとCAD技術を応用し、
3次元製品モデルを中心とした第2世代の「Symphony」「Jupiter]等のシステムがあります。
既に述べたように、両世代のシステムの最も大きな違いはモデル化の方法にあります。第1世代では数値データを机上で作成します。
鋼橋の線形上の格点を要素メッシュで分割することにより3次元サーフェースモデルが作られます。
一方、第2世代ではデータはCADで作成します。
ソリッドで構成される部品群を骨組線に沿ってスイープすることにより3次元形状ソリッドモデルが作られます。
両世代のシステム共3次元形状モデルを利用して工場製作の各フェーズに必要な製作情報を出力しますが、共通する課題は上流の設計システム、
下流の汎用CADとの情報連携です。
1)設計と製作情報の連携
図面をインターフェースとしたアナログ情報を製作で利用するためには、データの再入力が必要ですが、再入力ミスが生じる危険があります。
また、構造寸法が表で表されたり、省略作画される現状の図面は、デジタル情報であってもその情報を利用するには人間の介在が必要です。
そのため、設計情報をXML形式のデータフォーマットでデジタル化し、その情報を製作情報システムの入力データとして利用する仕組みが作られ、
情報の連携が図られています。
このフォーマットの標準化が望まれますが、現状では特定のCAD/CAM間のローカルな範囲に留まっています。
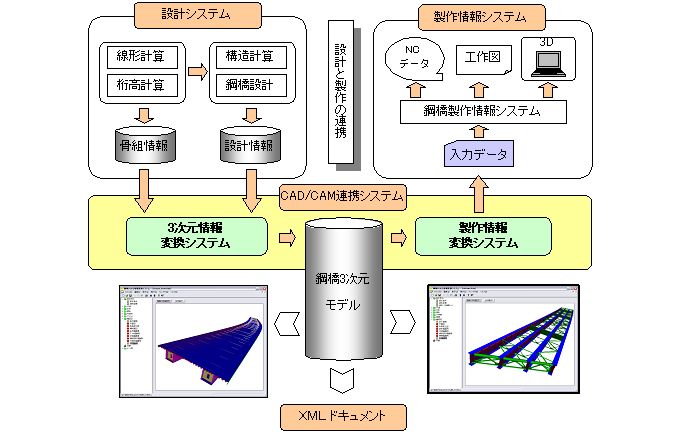
2)製作情報とCADの連携
製作情報システムは、工場設備、アウトソーシングの方法や作り方の違いによりアウトプットに様々なバリエーションが要求されます。
一つの製作情報システムで全ての情報が完結するのが理想ですが、橋梁の構造形式の違い、
システム上の制約や求められる出力の違いなどにより現実的ではありません。
一方でCADには白紙のカンバスに絵を描くような機能と、描かれた絵を様々に変換できる機能がありますが、
部材の展開やパラメトリックに変化する大量の図形の処理には適していません。
そのためほとんどの橋梁メーカーでは製作情報システムと汎用CADの2つを中核システムとして運用されていますが、
NC情報と図形情報の連携がネックになっていました。
NC情報は図形情報に意味を持たせたもので、CADで切断線と罫書線を色分けするようにテキストデータにラベルを付けます。
CADが一般的でなかった時代の智恵ですが、様々なNCフォーマット(CL/DL/FL/XCL)が独自に進化しガラパゴス化してきました。
そのため、NC情報と図形情報を統合した標準フォーマットとしてNCxmlが提案されています。
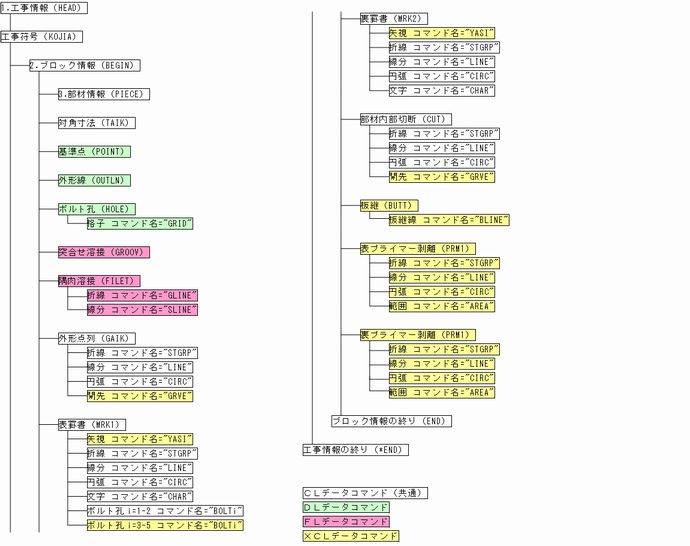
これまでに様々な製作情報システムが開発され、対象構造物の拡大を図りながら製作の標準化や生産性の向上に寄与してきました。 これらシステムに共通する基本機能は3次元のモデルを作りそこから平面の部品を作成することです。 これらの部品には形状情報の他に重量、板厚、材質等様々な属性情報があります。 製作情報システムでは形状情報の修正、変更に小回りが利かず、汎用のCADでは属性情報の取り扱いが困難です。 そこで、製作情報システムと汎用CADを繋ぐツールとして「SoftDraw」のようなCAD編集システムが利用されています。 様々なフォーマットのNC情報や図形情報を相互に変換し、形状や部材情報の修正、編集作業をサポートします。 今後の橋梁製作においては、既存の製作情報システム、汎用CAD、CAD編集システムが動的に運用され、 自社の文化に則したオーダーメードな製作情報の作成と生産管理が進んでいくものと考えられます。
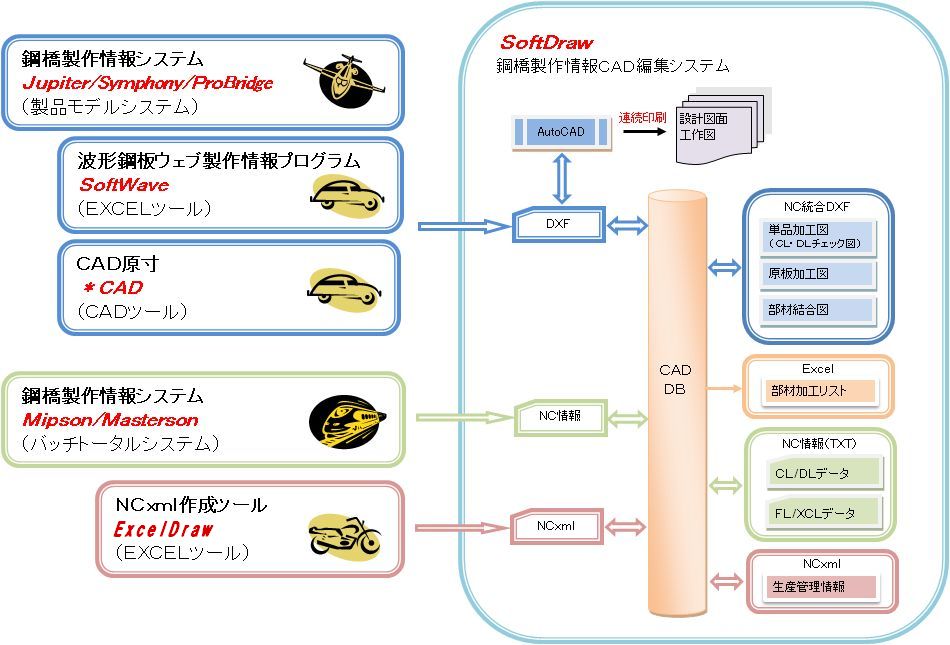